TECHNOLOGY AND THE CHARACTERISTICS OF OUR GALVANIZING PLANT
Hot-dip galvanizing is the application of a metallic zinc coating to iron or steel by immersing it in molten zinc (at around 450°). The zinc coating forms an inseparable alloy with the steel. Galvanizing is therefore ideal for all interior and exterior surfaces made of steel or iron and is cost-effective and environmentally friendly.
The durability of the hot-dip galvanized product depends on the respective environmental conditions. A zinc coating lasts 20 to 40 years, depending on the environmental conditions and atmosphere.
FEUERVERZINKUNGSNORMEN
EN ISO 1461
Zinc coatings fire dipped onto steel and alloy products – Specifications and test methods
EN ISO 14713
Iron and steel construction rust protection – zinc and aluminum coatings
EN 10240
Internal and/or external protective coatings on steel pipes – Requirements for hot-dip galvanized coatings using the dipping process in automated operations
EN 12502-1
Rust protection of metal materials – Instructions for determining the probability of rust occurrence in water supply and water storage systems – Part 1: General
EN 12502-3
Rust protection of metal materials – Instructions for determining the probability of rust occurrence in water supply and water storage systems – Part 3: Factors influencing hot-dip galvanized iron materials
EN 10244-2
Steel wires and wire products – Non-ferrous metallic coatings on steel wires – Part 2: Zinc and zinc alloy coatings
EN 10326
Sheet and strips made of structural steel, continuously hot-dip galvanized – Technical delivery conditions
EN 10327
Sheet and strips made of deep-drawn steel for cold forming, continuously hot-dip galvanized – Technical delivery conditions
EN 13811
Sherarding – Diffusion zinc coatings on iron products
ASTM A123 / A123M
Standard of technical conditions for zinc coatings (hot-dip galvanized) on alloy and steel products
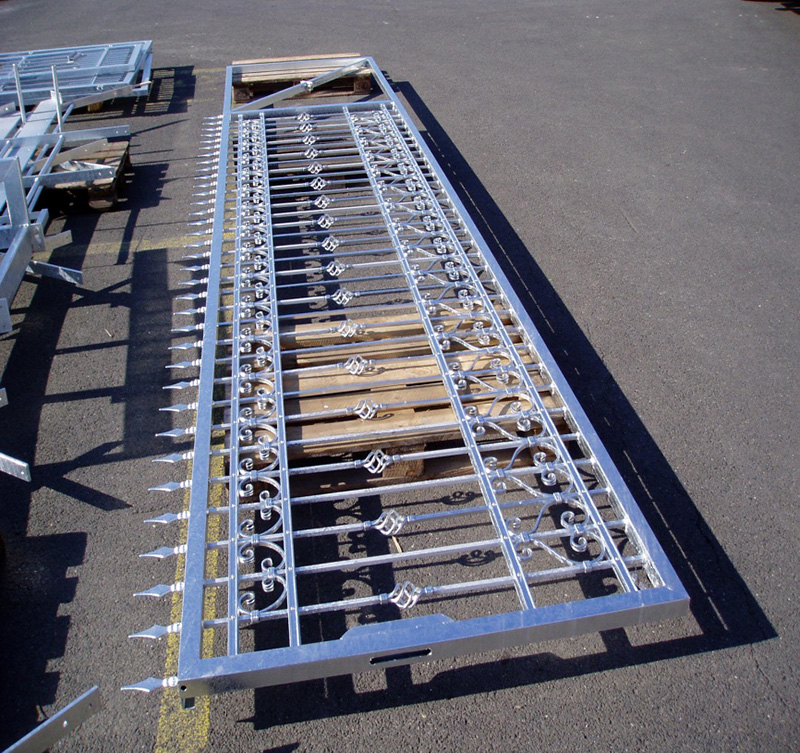
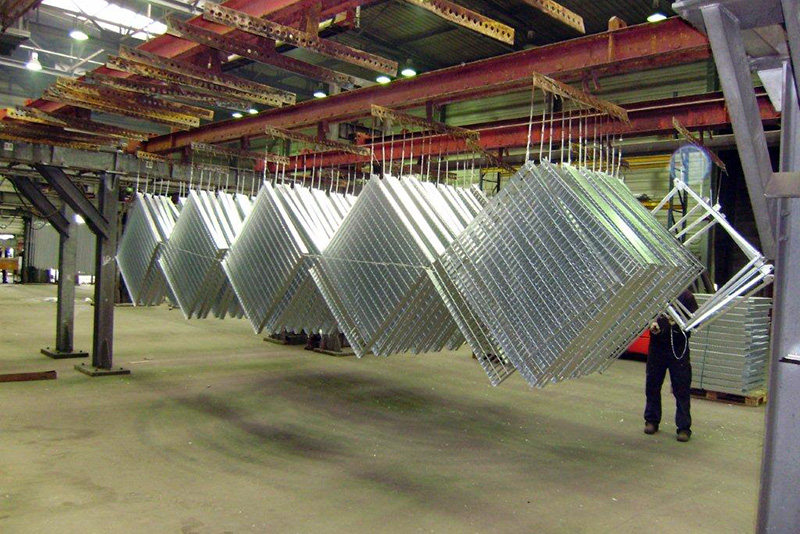